On the first weekend in August 2011, Monash University along with a number of other Victorian Universities held an Open Day, where visitors were encouraged to tour the facilities and learn about the courses offered there.
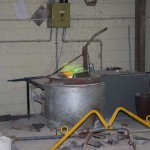
We were visiting the Caufield Campus of Monash University where we were privileged to observe a molten bronze pour in the Sculpture Department of the Visual Arts buildings.
Our guide through the process, Alex, was one of the technical staff actually involved the pour.
Click on any of the images in this article for an enlarged view.
This event was the culmination of up to six weeks work by the sculptors – creating the original master, preparing the mold using the lost wax technique, and baking the reinforced plaster mold in the kiln ready to receive the molten bronze.
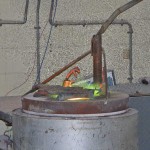
The gas fired, air injected furnace itself was noisily spewing green flames, a sure sign of vaporizing copper. Ingots of bronze and sprues from previous pours sat on the rim of the lid, waiting their turn to be placed in the crucible.
The heat radiating away from the crucible was captured much more dramatically in these images than was visible to the naked eye at the time.
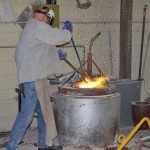
Periodically one of the pour team members, John, would add more bronze, skim impurities off the surface and check the crucible temperature using a high temperature probe placed briefly into the crucible, and connected to a wall mounted digital display.
The furnace heated the bronze-filled crucible to nearly 1200°C over the space of a few hours.
When Alex and John were satisfied the temperature was “right”, the noisy forced air injection was turned off and the lid moved aside. The crucible was lifted clear of the furnace using an ingenious hand operated lifting frame suspended from an overhead electric crane.
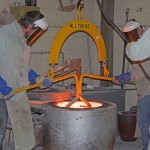
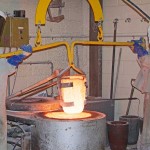
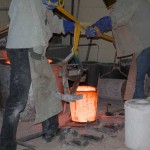
The glowing hot crucible was lowered into another frame and secured for the pour. It was a two man effort by Alex and John to guide the crucible, while the third member of the team, Evan, operated the overhead crane, following instructions from Alex.
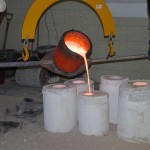
Alex judged, from years of experience, when the temperature and behavior of the molten bronze was suitable for pouring into the prepared molds. The best temperature varies depending on the nature of the object to be cast – it’s size, complexity and inherent characteristics. The last piece to be poured, also the largest, was described as “organic” and required a “cooler” pour.
The molds were all arranged on a bed of sand which provided a buffer for the molds and a soft, absorbent surface for any molten metal spills.
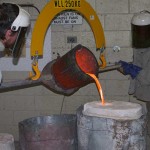
Watching the red hot bronze being poured into the molds was exhilarating.
With the time and effort required to prepare the original sculptures and their molds, the team usually try to have more molten bronze than necessary rather that run out part way through a pour. The extra molten bronze simply gets poured into molds to solidify into ingots for the next project.
At the end of the pour the crucible was returned to the safety of the now inactive, but still extremely hot, furnace. The molds meanwhile all had their filling sprue cups glowing with red hot bronze.
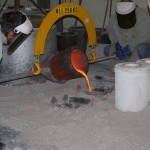
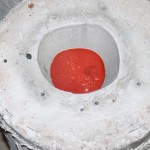
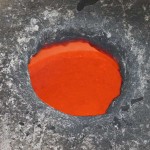
Alex then pulled over a mold that had been poured previously and was now well and truly set and cooled. He demonstrated how the mold was broken to safely release the sculpture and filling sprue.
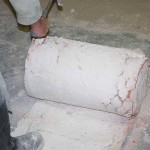
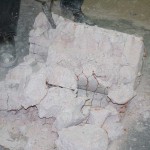
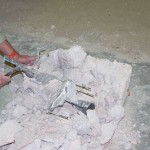
The sculptures however are not yet finished at this point. The sprue has to be cut off, and the surface repaired to match the rest of the sculpture as if the sprue had never existed. In the case of the sculpture Alex released, it had more work to be done to add a separately cast piece that was just too difficult to pour in the original mold.
Then the task of cleaning and applying the patina can start.
The sprue itself goes back for recycling in a future bronze pour.
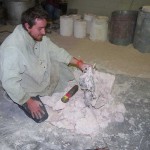
The journey from concept to final completed sculpture is long and involved. I feel privileged to have witnessed a small and spectacular part of that process.
A very big THANK YOU to Monash University – Caufield Campus, the Faculty of Art and Design, and especially to Alex, John and Evan.
And a special thank you to Rachael for inviting us.